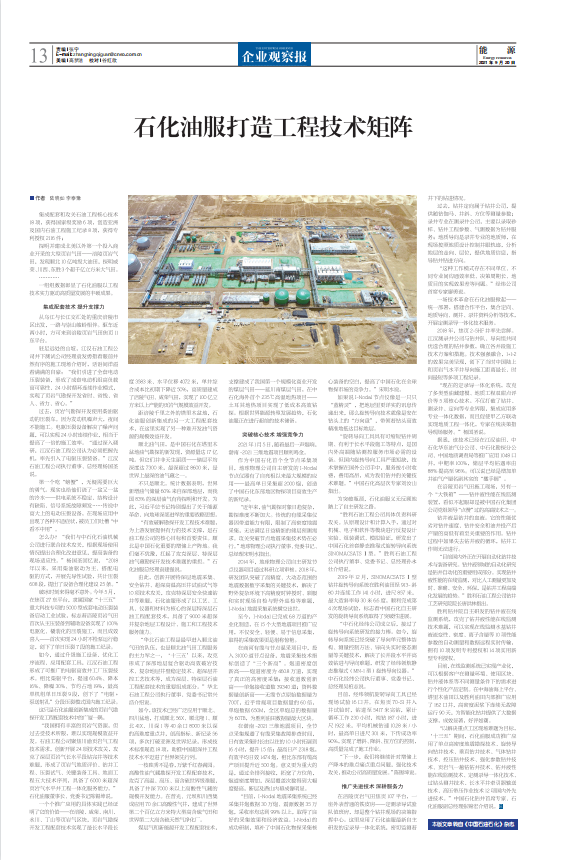
石化油服打造工程技术矩阵
集成配套和攻关石油工程核心技术18项,获得国家级奖励6项,创造亚洲及国内石油工程施工纪录8项,获得专利授权2116件;
探明并建成北美以外第一个投入商业开采的大型页岩气田——涪陵页岩气田,发现顺北10亿吨级大油田,探明威荣、川西、东胜3个超千亿立方米大气田。
…………
一组组数据彰显了石化油服以工程技术实力驱动高质量发展的丰硕成果。
集成配套技术 提升支撑力
从乌江与长江交汇处的重庆涪陵市区出发,一路与崇山峻岭相伴。驱车近两小时,方可来到涪陵页岩气田焦页11东平台。
驻足远处的山坡,江汉石油工程公司井下测试公司经理袁发勇指着眼前井然有序的施工现场介绍时,话语间洋溢着满满的自豪:“我们引进了全套电动压裂装备,形成了成套电动机组高负载高可靠性、24小时循环连续作业模式,实现了页岩气勘探开发省时、省钱、省人、省力、省心。”
过去,页岩气勘探开发使用柴油驱动的压裂车。因为发动机噪声大,夜间不能施工。电驱压裂设备解决了噪声问题,可以实现24小时连续作业,相当于提高了一倍的施工效率。“通过深入调研,江汉石油工程公司认为必须把握先机,率先引入了电驱压裂装备。”江汉石油工程公司执行董事、总经理杨国圣说。
第一个吃“螃蟹”,无疑需要巨大的勇气。现实也给他们浇了一盆又一盆的冷水——供电系统不稳定、结构设计有缺陷、信号系统故障频发……传说中高大上的电动压裂设备,在现场应用中出现了各种不适症状,被员工们吐槽“中看不中用”。
怎么办?“我们与中石化石油机械公司进行联合技术攻关,根据现场使用情况提出合理化改进意见,提高装备的现场适应性。”杨国圣回忆说,“2018年以来,采用柴油驱动为主、搭配电驱的方式,开展先导性试验,共计压裂608段,提出了设备合理化建议25条。”
破冰时刻来得毫不意外。今年5月,在焦页27东平台,隶属国家“十三五”重大科技专项的5000型成套电动压裂装备启动工业试验,标志着涪陵页岩气田首次从主压装备到辅助设备实现了100%电驱化、橇装化的压裂施工,而且成效喜人——首次实现24小时不检泵运行稳定,创下了单日压裂7段的施工纪录。
如今,通过升级施工设备、优化工序流程、应用配套工具,江汉石油工程形成了可推广的电驱高效井工厂压裂技术。相比柴驱平台,提速60.4%、降本16%、降噪30%、节约占地19%,最高单机组单日压裂9段,创下了“电驱+泵送射孔”分段压裂模式国内施工纪录。
这只是石化油服创新集成的页岩气勘探开发工程配套技术中的广厦一隅。
“我国拥有丰富的页岩气资源,但过去受技术所限,难以实现规模效益开发。石油工程公司聚焦川渝页岩气工程技术需求,创新开展24项技术攻关,攻克了深层页岩气长水平段钻完井等技术难题,形成了页岩气地质评价、钻井工程、压裂试气、关键装备工具、地面工程五大技术序列,具备了6000米超深页岩气水平井工程一体化服务能力。”石化油服董事长、党委书记陈锡坤说。
一个个推广应用的具体实践已经证明了它的价值——在涪陵、威荣、南川、永川、丁山等页岩气区块,页岩气勘探开发工程配套技术实现了最长水平段长度3583米、水平位移4072米,单井综合成本比初期下降近50%,高质量建成了涪陵气田、威荣气田,实现了100亿立方米以上产能的页岩气规模效益开发。
距涪陵千里之外的塔里木盆地,石化油服创新集成的另一大工程配套技术,在这里实现了另一种难开发油气资源的规模效益开发。
顺北油气田,是中国石化在塔里木盆地油气勘探的新发现,资源量达17亿吨。但它们并非天生丽质——储层平均深度达7300米,最深超过8600米,是世界上最深的油气藏之一。
不只是顺北。统计数据表明,世界新增油气储量60%来自深部地层,而我国83%的深层油气有待探明和开发。为此,习近平总书记特别提出了关于能源革命、向地球深部进军的重要战略思想。
“有效破解勘探开发工程技术难题,为上游发展提供有力的技术支撑,是石油工程公司的核心目标和首要责任。顺北是中国石化重要的增储上产阵地。我们毫不犹豫,扛起了攻克深层、特深层油气藏勘探开发技术难题的重担。”石化油服总经理袁建强说。
由此,创新开展特深层地震采集、安全钻井、超深高温高压井试油试气等10项技术攻关,攻克特深层安全快速钻井等难题,石化油服形成了以工艺、工具、仪器和材料为核心的深层特深层石油工程配套技术,具备了9000米超深井复杂地层工程设计、施工和工程技术服务能力。
“华北石油工程是最早进入顺北油气田的队伍,也是顺北油气田工程服务的主力军之一,‘十三五’以来,攻克形成了深部地层复合驱动高效破岩技术、复杂地层井壁稳定技术、超深层井控工艺技术等,成为深层、特深层石油工程配套技术的重要组成部分。”华北石油工程公司执行董事、党委书记常兴浩介绍说。
如今,该技术已经广泛应用于顺北、四川盆地,打成顺北56X、顺北隆1、顺北41X、川深1等40余口8000米以深的高难度重点井,创高指标、新纪录56项,多次打破亚洲及世界纪录,形成技术标准规范18项,助推中国超深井工程技术水平迈进了世界领先行列。
一枝独秀不是春,万紫千红春满园。高酸性油气藏勘探开发工程配套技术,攻克了高温、高压、高含硫世界级难题,具备了井深7000米以上高酸性气藏的规模开发能力。在普光、元坝和川西集成应用70余口高酸性气井,建成了世界第二个百亿立方米特大型高含硫气田和世界第二大高含硫天然气净化厂。
煤层气和新能源开发工程配套技术,支撑建成了我国第一个规模化商业开发的煤层气田——延川南煤层气田,在中石化海外首个235℃高温地热项目——土耳其地热项目实现了低成本高效钻探。根据世界能源转型发展趋势,石化油服正在进行超前的技术储备。
突破核心技术 增强竞争力
2021年1月5日,随着最后一声炮响,渤南-2021三维地震项目顺利鸣金。
作为中国石化首个全节点采集项目,地球物理公司自主研发的I-Nodal节点仪器有了自亮相以来最大规模的应用——最高单日采集超2000炮,创造了中国石化东部地区物探项目高效生产的新纪录。
“近年来,油气勘探对象日趋复杂,勘探难度不断加大。传统的有缆采集仪器因带道能力有限,限制了高密度地震采集,无法满足日益精细的储层预测需求。攻关突破节点地震采集技术势在必行。”地球物理公司执行董事、党委书记、总经理宋明水指出。
2014年,地球物理公司自主研发节点仪器项目通过科研立项审核。2018年,研发团队突破了高精度、大动态范围的地震数据数字采集的关键技术,解决了野外复杂环境下高精度时钟授时、驯服和实时现场自检与野外巡检等难题,I-Nodal地震采集系统横空出世。
至今,I-Nodal已完成6.8万道的产业化制造,在15个大型地震项目推广应用,不仅安全、轻便、易于信息采集,取得的采集效果更是堪称惊艳。
在商河有缆与节点混采项目中,投入31000道节点设备,地震采集技术指标创造了“三个新高”。炮道密度创新高——炮道密度为460.8万道,实现了真正的高密度采集;接收道数创新高——单炮接收道数39340道;资料数据量创新高——无缆节点原始数据量为700T,近乎常规项目数据量的60倍,单炮数据650M,全区单炮总的数据量为60TB,为胜利油田数据量最大区块。
在渤南-2021三维地震项目,全节点采集规避了有缆采集故障排查时间,日有效采集时长由以往的10小时拓展到16小时,提升1.5倍;最高日产2318炮,有效平均日效1474炮,相比东部有缆高产项目提升近500炮。意义更为重大的是,通过全排列接收,拓宽了方位角,炮道密度增加,深层覆盖次数得到大幅度提高,断层及潜山内幕成像明显。
“目前,I-Nodal地震采集系统已经采集井炮数据30万炮、震源数据35万炮,采收率均达到99%以上,取得了良好的采集效果和经济效益。I-Nodal的成功研制,填补了中国石化物探采集核心装备的空白,提高了中国石化在全球物探市场的竞争力。”宋明水说。
如果说I-Nodal节点仪像是一只只“蓝精灵”,把地层里更详实的讯息传递出来,那么旋转导向技术就像是安在钻头上的“方向盘”,带领着钻头高效精准地抵达目标地层。
“旋转导向工具具有可缩短钻井周期、有利于长水平段施工等特点,是国内外高端随钻测控服务市场必需的设备。但国内旋转导向工具严重短缺,技术掌握在国外公司手中,服务按小时收费,费用高昂,成为我们钻井的关键技术难题。”中国石化高层次专家刘汝山指出。
为突破瓶颈,石化油服义无反顾地踏上了自主研发之路。
“胜利石油工程公司具体负责科研攻关。从原理设计和计算入手,通过对机械、电子和软件等模块进行反复设计实验、组装调试、模拟验证,研发出了中国石化首套静态推靠式旋转导向系统SINOMACSATSⅠ型。”胜利石油工程公司执行董事、党委书记、总经理孙永壮介绍说。
2019年12月,SINOMACSATSⅠ型钻井旋转导向系统在胜利油田埕913-斜80井连续工作141小时,进尺857米,最大造斜率每30米6.6度,顺利完成第4次现场试验,标志着中国石化自主研发的旋转导向系统取得了突破性进展。
“中石化经纬公司成立后,接过了旋转导向系统研发的接力棒。如今,旋转导向系统已经突破了导向单元整体结构、测量控制方法、导向头实时姿态测量等关键技术,解决了长井段水平井高效钻进与导向难题,研发了经纬领航静态推靠式(MN-1型)旋转导向仪器。”中石化经纬公司执行董事、党委书记、总经理吴柏志说。
目前,经纬领航旋转导向工具已经现场试验16口井。在焦页70-S1井入井试验时,钻进至5417米完钻,累计循环工作230小时,纯钻187小时,进尺1922米,平均机械钻速10.28米/小时,最高单日进尺301米,下传成功率90%,实现了增斜、降斜、扭方位的控制,高质量完成了施工作业。
“下一步,我们将继续针对增储上产降本的难点痛点重点问题,强化技术攻关,推动公司高质量发展。”陈锡坤说。
推广先进技术 深耕服务力
在涪陵页岩气田焦页107平台,一座外表普通的铁皮房——定测录导试验队值班房,却是整个钻井现场的决策指挥中心。这里应用了石化油服最新自主研发的定录导一体化系统,密切监测着井下的钻进情况。
过去,钻井定向属于钻井公司,提供随钻伽马、井斜、方位等测量参数;录井专业在测录井公司,主要以录取砂样、钻井工程参数、气测数据为钻井服务;地质导向是录井专业的地质师,在现场按照地质设计控制井眼轨迹,分析地层的走向、层位,提供地质信息,指导钻井钻进方向。
“这种工作模式存在不同单位、不同专业间沟通效率低、决策周期长、地质目的实现效果差等问题。”经纬公司首席专家廖勇说。
一场技术革命在石化油服掀起——统一部署,搭建合作平台,集合定向、地质导向、测井、录井资料分析等技术,开展定测录导一体化技术服务。
2018年,焦页2-5HF井率先尝鲜。江汉测录井公司与钻井队、导向组共同优选合理的钻井参数,确立各井段施工技术方案和措施。技术强强融合,1+1>2的效果完美呈现,创下了当时中国陆上和页岩气水平井导向施工距离最长、时间最短等多项工程纪录。
“现在的定录导一体化系统,攻克了多类型油藏建模、地质工程双甜点评价等5项核心技术。不仅打破了钻井、测录井、定向等专业界限,集成应用多专业一体化数据,而且促使甲乙方联动实现地质工程一体化,专家在线决策指导现场服务。”杨国圣说。
据悉,该技术已经在江汉油田、中石化华东油气分公司、中石化勘探分公司、中国地质调查局等推广应用1048口井,中靶率100%,储层平均钻遇率由88%提高至96%。可以说已经是增加单井油气产量名副其实的“撒手锏”。
在涪陵页岩气田施工现场,另有一个“大铁箱”——钻井液性能在线监测装置,看似不起眼却是被中国石化集团公司党组领导“点赞”过的高端技术之一。
钻井液是钻井的血液。它的性能优劣对钻井速度、钻井安全和油井投产后产量的高低有着至关重要的作用。钻井过程中如果失去钻井液的循环,钻井工作则无法进行。
“目前国内外正在开展自动化钻井技术与装备研究。钻井液领域的自动化研究是钻井自动化的重要组成部分。实现钻井液性能的在线监测,对比人工测量更加及时、准确、安全、环保,是钻井工程高端化发展的趋势。”胜利石油工程公司钻井工艺研究院院长唐洪林指出。
胜利钻井院自主研发的钻井液在线监测系统,攻克了钻井液性能在线监测技术难题,可以实现在线监测水基钻井液流变性、密度、离子含量等10项性能参数的自动测量和数据远程实时传输,拥有10项发明专利授权和14项实用新型专利授权。
目前,在线监测系统已实现产业化,可以根据客户在测量环境、使用区块、钻井液体系等不同测量条件下的需求进行个性化产品定制。在中海油海上平台、塔里木油田以及胜利油田内部推广应用了162口井,高密度泥浆下连续无故障运行90天,为智能化钻井提供了大数据支撑,成效显著,好评如潮。
“以解决重点工区现场难题为目标,‘十三五’期间,石化油服成功推广应用了单点高密度地震勘探技术、旋转导向钻井技术、垂直钻井技术、气体钻井技术、控压钻井技术、强化参数钻井技术、页岩气一趟钻钻井技术、钻井液性能在线监测技术、定测录导一体化技术、过钻头测井技术、长水平井牵引器输送技术、高压带压作业技术12项国内外先进技术。”中国石化钻井首席专家、石化油服副总经理张锦宏介绍说。