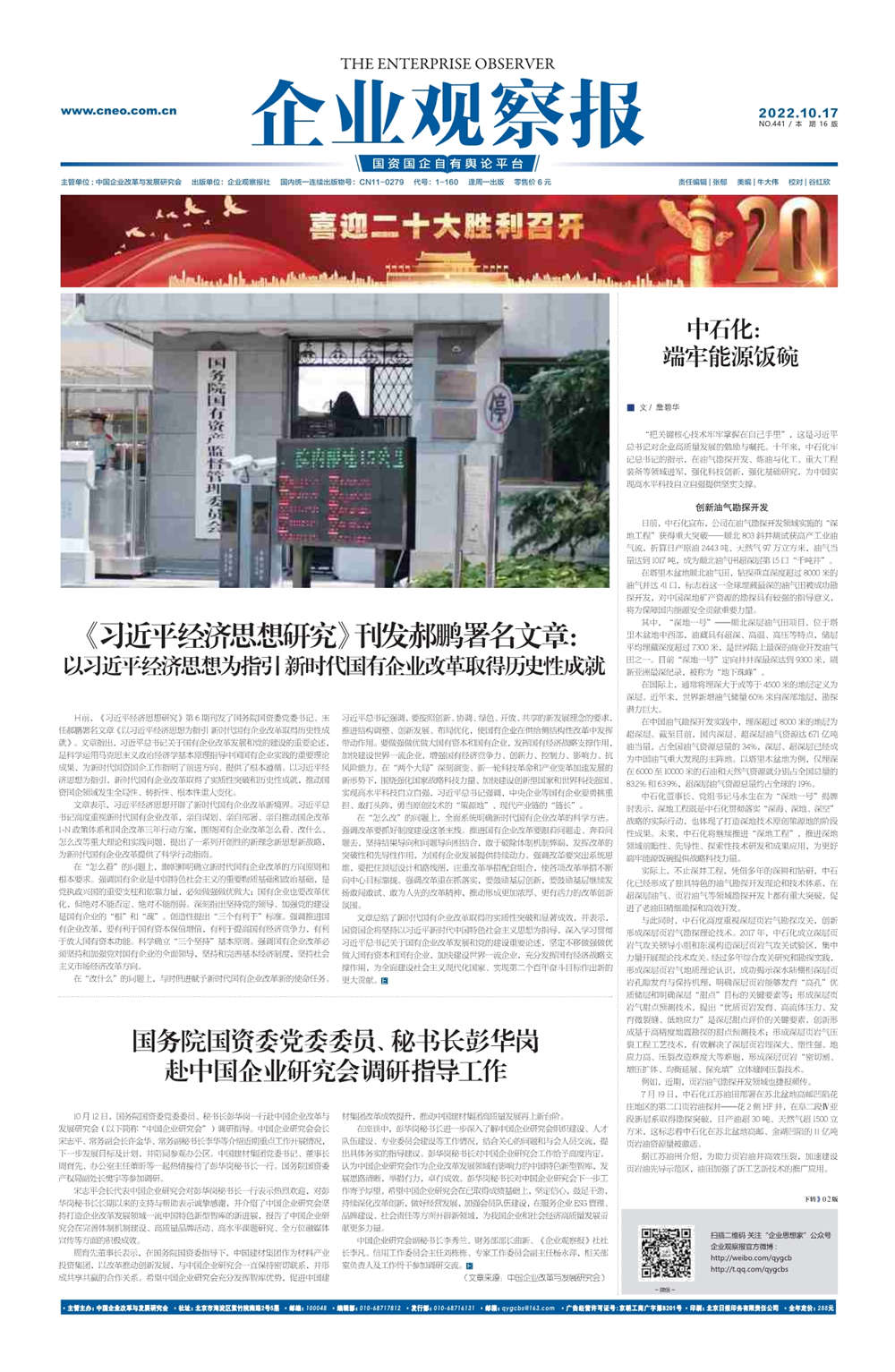
中石化: 端牢能源饭碗
“把关键核心技术牢牢掌握在自己手里”,这是习近平总书记对企业高质量发展的勉励与嘱托。十年来,中石化牢记总书记的指示,在油气勘探开发、炼油与化工、重大工程装备等领域进军,强化科技创新,强化基础研究,为中国实现高水平科技自立自强提供坚实支撑。
创新油气勘探开发
日前,中石化宣布,公司在油气勘探开发领域实施的“深地工程”获得重大突破——顺北803斜井测试获高产工业油气流,折算日产原油244.3吨、天然气97万立方米,油气当量达到1017吨,成为顺北油气田超深层第15口“千吨井”。
在塔里木盆地顺北油气田,钻探垂直深度超过8000米的油气井达41口,标志着这一全球埋藏最深的油气田被成功勘探开发,对中国深地矿产资源的勘探具有较强的指导意义,将为保障国内能源安全贡献重要力量。
其中,“深地一号”——顺北深层油气田项目,位于塔里木盆地中西部,油藏具有超深、高温、高压等特点,储层平均埋藏深度超过7300米,是世界陆上最深的商业开发油气田之一。目前“深地一号”定向井井深最深达到9300米,刷新亚洲最深纪录,被称为“地下珠峰”。
在国际上,通常将埋深大于或等于4500米的地层定义为深层。近年来,世界新增油气储量60%来自深部地层,勘探潜力巨大。
在中国油气勘探开发实践中,埋深超过8000米的地层为超深层。截至目前,国内深层、超深层油气资源达671亿吨油当量,占全国油气资源总量的34%,深层、超深层已经成为中国油气重大发现的主阵地。以塔里木盆地为例,仅埋深在6000至10000米的石油和天然气资源就分别占全国总量的83.2%和63.9%,超深层油气资源总量约占全球的19%。
中石化董事长、党组书记马永生在为“深地一号”揭牌时表示,深地工程既是中石化贯彻落实“深海、深地、深空”战略的实际行动,也体现了打造深地技术原创策源地的阶段性成果。未来,中石化将继续推进“深地工程”,推进深地领域前瞻性、先导性、探索性技术研发和成果应用,为更好端牢能源饭碗提供战略科技力量。
实际上,不止深井工程,凭借多年的深耕和钻研,中石化已经形成了独具特色的油气勘探开发理论和技术体系,在超深层油气、页岩油气等领域勘探开发上都有重大突破,促进了老油田精细勘探和高效开发。
与此同时,中石化高度重视深层页岩气勘探攻关,创新形成深层页岩气勘探理论技术。2017年,中石化成立深层页岩气攻关领导小组和东溪构造深层页岩气攻关试验区,集中力量开展理论技术攻关。经过多年综合攻关研究和勘探实践,形成深层页岩气地质理论认识,成功揭示深水陆棚相深层页岩孔隙发育与保持机理,明确深层页岩能够发育“高孔”优质储层和明确深层“甜点”目标的关键要素等;形成深层页岩气甜点预测技术,提出“优质页岩发育、高流体压力、发育微裂缝、低地应力”是深层甜点评价的关键要素,创新形成基于高精度地震勘探的甜点预测技术;形成深层页岩气压裂工程工艺技术,有效解决了深层页岩埋深大、塑性强、地应力高、压裂改造难度大等难题,形成深层页岩“密切割、增压扩体、均衡延展、保充填”立体缝网压裂技术。
例如,近期,页岩油气勘探开发领域也捷报频传。
7月19日,中石化江苏油田部署在苏北盆地高邮凹陷花庄地区的第二口页岩油探井——花2侧HF井,在阜二段Ⅳ亚段新层系取得勘探突破,日产油超30吨、天然气超1500立方米,这标志着中石化在苏北盆地高邮、金湖凹陷的11亿吨页岩油资源量被激活。
据江苏油田介绍,为助力页岩油井高效压裂,加速建设页岩油先导示范区,油田加强了新工艺新技术的推广应用。
花2侧HF井压裂采用水平井密切割体积压裂施工设计,压裂水平段长1077.4米,全井分20段压裂,加砂量2362.8立方米。
为提高非常规压裂增产提效水平,工程技术人员加强地质工程一体化研究,结合储层纵向应力特征,开展“一段一策”差异化设计。
压裂方案上,通过采用“多段多簇密切割布缝、一体化变黏滑溜水体系、大规模压裂全尺度支撑”的压裂方案,提高改造体积。施工模式上,应用“渗析洗油+压注补能+闭合暂堵转向”施工模式,提高页岩油井采收率水平。
为有效降低压裂成本,油田首次应用电驱压裂技术,取代传统的柴油发动机驱动压裂。
8月25日,中石化胜利油田济阳陆相断陷湖盆页岩油国家级示范区揭牌。预计该示范区将实现页岩油探明地质储量1亿吨,新建产能100万吨,年产页岩油当量50万吨。中石化称,该示范区预期将形成六方面示范成果,包括页岩油基础理论示范、地质评价技术示范、开发技术示范、一体化运行模式示范等。
突破炼化领域“卡脖子”技术
“十四五”时期,能源面临低碳转型的新趋势,这对炼油与石化产业发展带来新的挑战。
从企业层面来看,要向炼化一体化和油转化升级,加快淘汰落后炼油能力,大力推进原油高效加工利用技术、清洁高效汽柴油生产技术、炼油过程节能环保技术、智能化炼油厂构建技术、生物质炼制生产液体燃料技术、二氧化碳捕集利用技术等新技术的研发应用。要围绕绿色低碳提质增效,积极采用新技术和新装备,实施已有炼油企业原油利用高效化、炼油过程绿色低碳化、产出油品高效清洁化的技术改造。
在炼化技术方面,中石化掌握了比肩世界先进水平的炼油全流程技术,在重油催化裂化、加氢裂化、催化裂解、催化汽油吸附脱硫、柴油超深度加氢脱硫等技术上都有突破,成功开发了烷基化、异构化技术及高端润滑油合成基础油等特种油品生产工艺,满足了汽柴油质量标准从国3到国6的升级技术需求。
目前炼化企业由燃料型向化工型炼厂转型最关键的两项技术是催化裂解技术和加氢裂化技术。以催化裂解技术为核心的无油炼厂,千万吨原油可以生产出400万吨的烯烃、200万吨的芳烃和约150万吨的低硫船燃。这一过程中的关键技术,比如石脑油、航煤和柴油的催化裂解技术、原油催化裂解技术、加氢渣油催化裂解技术,已经有一些比较好的结果,未来要持续攻关。
在炼油结构转型及升级方面,中石化锚定“油转化”“油产化”和“油转特”发展方向,以天津石化为例,今年,天津石化在大港片区投资逾10亿元,加快实施“油转化”技术改造项目。其中,在增产化工原料方面,该公司通过对2号常减压装置进行适应性改造,达到压减柴油产量、增产石脑油的目的;在化工原料调优方面,天津石化对2号柴油加氢装置进行改造,以生产优质的乙烯原料。此外,天津石化将过剩的低价值混合碳四通过催化裂解,把碳四烯烃转化为高价值丙烯和富乙烯气,作为下游化工原料,有效缓解了乙烯原料短缺的矛盾。
与此同时,金陵石化充分利用炼油装置数量多、种类全、灵活性大的结构特点,推进老装置改造升级,加快“油转特”步伐,2021年,该公司对原有延迟焦化装置进行改造,成功建成系统内首套高端石墨材料装置,并产出了高品质油系针状焦。该产品经煅烧后可供下游企业生产超高功率石墨电极和新能源汽车锂电池电极材料,与此前高硫焦相比,价格上涨了近4倍,已成为企业新的效益增长点。
在新能源方面,中石化也积极探索新能源与传统能源耦合一体化发展模式,聚焦CO2回收利用、“热氢风光”等绿色低碳新能源领域研究。其中,精心规划设计的3座加氢站顺利投用,为赋能“绿色冬奥”做出特有贡献;全球最大绿氢项目——新疆库车光伏制氢示范项目稳步推进,中科分布式光伏项目成功并网,多座加油(气)站屋顶光伏项目建设成功并投入发电,为能源产业节能减排和绿色发展提供助力。
在化工新材料等方面,中石化也聚焦“卡脖子”难题,以高水平的工程研发和工程转化能力补齐炼化产业链关键环节。
例如,中石化上海石化研发试产的大丝束碳纤维是一种含碳量95%以上的高强度新型纤维材料,其力学性能优异,比重不到钢的四分之一,强度却是钢的7-9倍,并且还具有耐腐蚀的特性,被称为“新材料之王”,也被称为“黑黄金”。碳纤维技术壁垒较高,迄今只有日本、美国等少数发达国家拥有并掌握。
持续推进关键设备国产化
今年3月份,全国人大代表、中石化石油工程技术研究院党委书记刘宝增在全国两会上表示,当前中国石油石化重大技术装备取得了令人瞩目的成就,中石化重大装备基本实现国产化。
近年来,中石化通过自主研发生产和联合国内企业协同研发生产等方式,持续加大重大装备国产化攻关力度。经过多年的深耕实践,中石化已从30多年前关键设备的一颗螺丝钉都要进口,发展到如今重大装备基本实现国产化。
截至“十三五”末,中石化重大装备国产化率创新高,基本实现国产化,其中,油气勘探开发装备国产化率达92%,千万吨级炼油装备国产化率达94%,百万吨级乙烯装备国产化率达87%。
乙烯裂解炉是乙烯工业的龙头装备,实现从引进到出口的转变。1988年,中国石化工程建设公司、北京化工研究院和兰州化机院成功研制首台国产2万吨/年乙烯裂解炉,结束乙烯裂解炉全部依靠引进的历史。2011年,中国石化工程建设公司、物资装备部(国际事业公司)与国内制造厂合作,向马来西亚泰坦项目出口首台10万吨/年乙烯裂解炉。2020年9月,中科炼化一体化项目全面进入开车阶段,乙烯“三机”(裂解气压缩机组、乙烯制冷压缩机组、丙烯制冷压缩机组)、挤压造粒机组、EO反应器等重大装备全部实现国产化,与进口设备相比,大幅节约采购资金,缩短制造周期30%。
此外,在电动压裂装备、高端钻头、大型加氢反应器、大型乙烯裂解气压缩机组、丙烯制冷压缩机组、大型挤压造粒机组、乙烯冷箱、大型炼油装置DCS等工程装备方面,中石化都具有世界先进水平的装备持续取得突破,有力地促进了中国制造业的发展。
近日,中石化方面还表示,将加大技术攻关力度,力争在高性能燃料电池催化等石化材料、质子交换膜电解水制氢、加氢站关键设备国产化等领域实现更大突破,为实现氢能产业链自主可控作出更大贡献。此外,聚焦产业链薄弱环节,构筑以骨干企业为牵引、高校院所联合攻关的创新联合体,积极引导搭建国家级创新平台,着力构建高效协作创新网络,共同推动氢能技术与装备国产化进程。