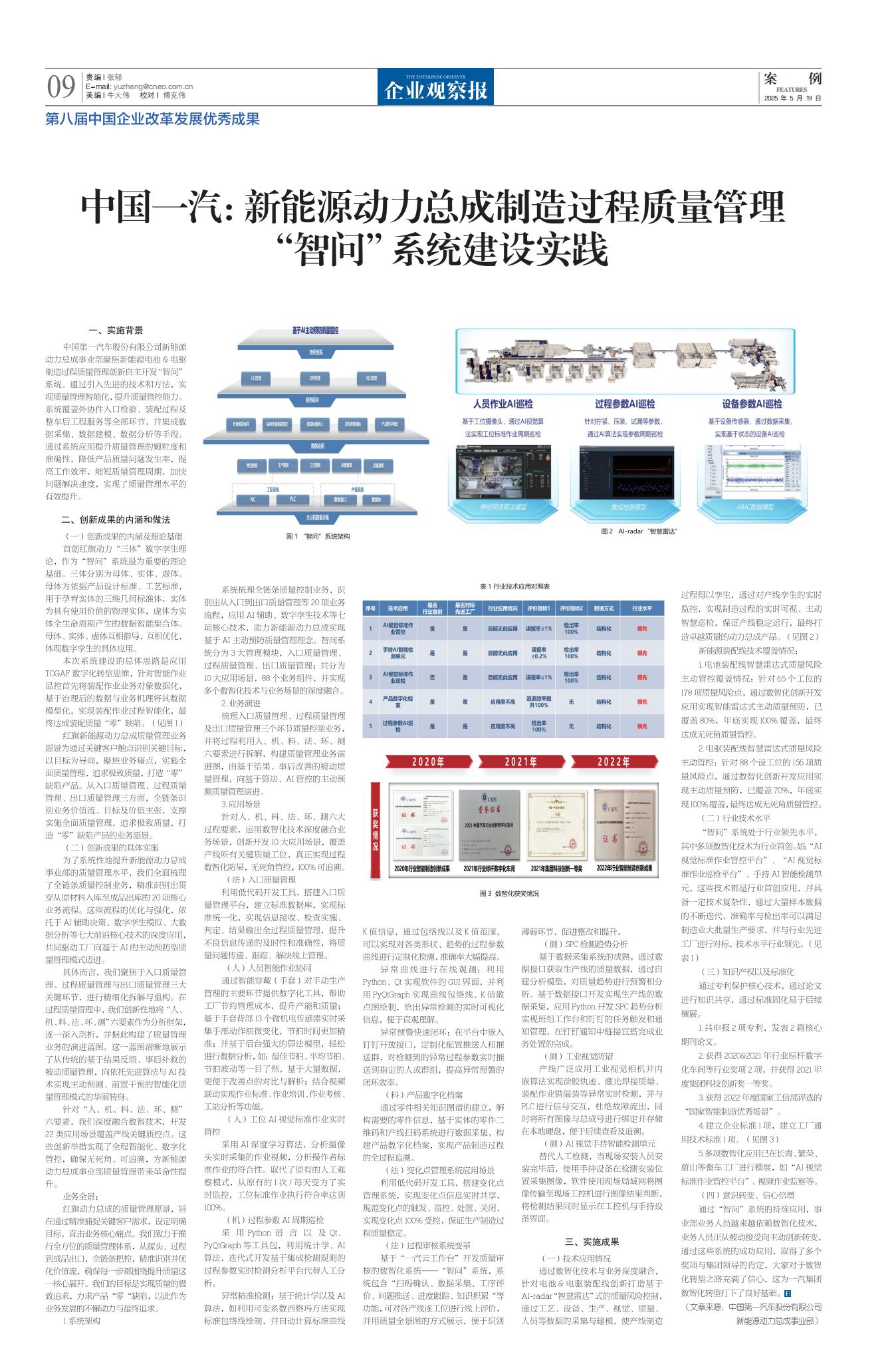
中国一汽:新能源动力总成制造过程质量管理 “智问”系统建设实践
一、实施背景
中国第一汽车股份有限公司新能源动力总成事业部聚焦新能源电池&电驱制造过程质量管理创新自主开发“智问”系统。通过引入先进的技术和方法,实现质量管理智能化,提升质量管控能力。系统覆盖外协件入口检验、装配过程及整车后工程服务等全部环节,并集成数据采集、数据建模、数据分析等手段。通过系统应用提升质量管理的颗粒度和准确性,降低产品质量问题发生率,提高工作效率,缩短质量管理周期,加快问题解决速度,实现了质量管理水平的有效提升。
二、创新成果的内涵和做法
(一)创新成果的内涵及理论基础
首创红旗动力“三体”数字孪生理论,作为“智问”系统最为重要的理论基础。三体分别为母体、实体、虚体。母体为依据产品设计标准、工艺标准,用于孕育实体的三维几何标准体,实体为具有使用价值的物理实体,虚体为实体全生命周期产生的数据智能集合体。母体、实体、虚体互相指导,互相优化,体现数字孪生的具体应用。
本次系统建设的总体思路是应用TOGAF数字化转型思维,针对智能作业品控首先将装配作业业务对象数据化,基于治理后的数据与业务机理将其数据模型化,实现装配作业过程智能化,最终达成装配质量“零”缺陷。(见图1)
红旗新能源动力总成质量管理业务愿景为通过关键客户触点识别关键目标,以目标为导向,聚焦业务痛点,实施全面质量管理,追求极致质量,打造“零”缺陷产品。从入口质量管理、过程质量管理、出口质量管理三方面,全链条识别业务价值流、目标及价值主张,支撑实施全面质量管理,追求极致质量,打造“零”缺陷产品的业务愿景。
(二)创新成果的具体实施
为了系统性地提升新能源动力总成事业部的质量管理水平,我们全面梳理了全链条质量控制业务,精准识别出贯穿从原材料入库至成品出库的20项核心业务流程。这些流程的优化与强化,依托于AI辅助决策、数字孪生模拟、大数据分析等七大前沿核心技术的深度应用,共同驱动工厂向基于AI的主动预防型质量管理模式迈进。
具体而言,我们聚焦于入口质量管理、过程质量管理与出口质量管理三大关键环节,进行精细化拆解与重构。在过程质量管理中,我们创新性地将“人、机、料、法、环、测”六要素作为分析框架,逐一深入剖析,并据此构建了质量管理业务的演进蓝图。这一蓝图清晰地展示了从传统的基于结果反馈、事后补救的被动质量管理,向依托先进算法与AI技术实现主动预测、前置干预的智能化质量管理模式的华丽转身。
针对“人、机、料、法、环、测”六要素,我们深度融合数智技术,开发22类应用场景覆盖产线关键质控点。这些创新举措实现了全程智能化、数字化管控,确保无死角、可追溯,为新能源动力总成事业部质量管理带来革命性提升。
业务全景:
红旗动力总成的质量管理愿景,旨在通过精准捕捉关键客户需求,设定明确目标,直击业务核心痛点。我们致力于推行全方位的质量管理体系,从源头、过程到成品出口,全链条把控,精准识别并优化价值流,确保每一步都围绕提升质量这一核心展开。我们的目标是实现质量的极致追求,力求产品“零“缺陷,以此作为业务发展的不懈动力与最终追求。
1.系统架构
系统梳理全链条质量控制业务,识别出从入口到出口质量管理等20项业务流程,应用AI辅助、数字孪生技术等七项核心技术,助力新能源动力总成实现基于AI主动预防质量管理理念。智问系统分为3大管理模块,入口质量管理、过程质量管理、出口质量管理;共分为10大应用场景,88个业务组件,并实现多个数智化技术与业务场景的深度融合。
2.业务演进
梳理入口质量管理、过程质量管理及出口质量管理三个环节质量控制业务,并将过程利用人、机、料、法、环、测六要素进行拆解,构建质量管理业务演进图,由基于结果、事后改善的被动质量管理,向基于算法、AI管控的主动预测质量管理演进。
3.应用场景
针对人、机、料、法、环、测六大过程要素,运用数智化技术深度融合业务场景,创新开发10大应用场景,覆盖产线所有关键质量工位,真正实现过程数智化防呆,无死角管控,100%可追溯。
(法)入口质量管理
利用低代码开发工具,搭建入口质量管理平台,建立标准数据库,实现标准统一化,实现信息接收、检查实施、判定、结果输出全过程质量管理,提升不良信息传递的及时性和准确性,将质量问题传递、跟踪、解决线上管理。
(人)人员智能作业协同
通过智能穿戴(手套)对手动生产管理的主要环节提供数字化工具,帮助工厂节约管理成本,提升产能和质量;基于手套背部13个微机电传感器实时采集手部动作细微变化,节拍时间更加精准;并基于后台强大的算法模型,轻松进行数据分析,如:最佳节拍、平均节拍、节拍波动等一目了然,基于大量数据,更便于改善点的对比与解析;结合视频联动实现作业标准、作业培训、作业考核、工站分析等功能。
(人)工位AI视觉标准作业实时管控
采用AI深度学习算法,分析摄像头实时采集的作业视频,分析操作者标准作业的符合性。取代了原有的人工观察模式,从原有的1次/每天变为了实时监控,工位标准作业执行符合率达到100%。
(机)过程参数AI周期巡检
采用Python语言以及Qt、PyQtGraph等工具包,利用统计学、AI算法,迭代式开发基于集成检测规则的过程参数实时检测分析平台代替人工分析。
异常精准检测:基于统计学以及AI算法,如利用可变系数西格玛方法实现标准包络线绘制,并自动计算标准曲线K值信息,通过包络线以及K值范围,可以实现对各类形状、趋势的过程参数曲线进行定制化检测,准确率大幅提高。
异常曲线进行在线观测:利用Python、Qt实现软件的GUI界面,并利用PyQtGraph实现曲线包络线、K值散点图绘制,给出异常检测的实时可视化信息,便于直观理解。
异常预警快速闭环:在平台中嵌入钉钉开放接口,定制化配置推送人和推送群,对检测到的异常过程参数实时推送到指定的人或群组,提高异常预警的闭环效率。
(料)产品数字化档案
通过零件相关知识图谱的建立,解构需要的零件信息,基于实体的零件二维码和产线扫码系统进行数据采集,构建产品数字化档案,实现产品制造过程的全过程追溯。
(法)变化点管理系统应用场景
利用低代码开发工具,搭建变化点管理系统,实现变化点信息实时共享,规范变化点的触发、监控、处置、关闭,实现变化点100%受控,保证生产制造过程质量稳定。
(法)过程审核系统变革
基于“一汽云工作台”开发质量审核的数智化系统—“智问”系统,系统包含“扫码确认、数据采集、工序评价、问题推送、进度跟踪、知识积累“等功能,可对各产线逐工位进行线上评价,并用质量全景图的方式展示,便于识别薄弱环节,促进整改和提升。
(测)SPC检测趋势分析
基于数据采集系统的成熟,通过数据接口获取生产线的质量数据,通过自建分析模型,对质量趋势进行预警和分析。基于数据接口开发实现生产线的数据采集,应用Python开发SPC趋势分析实现班组工作台和钉钉的任务触发和通知管理,在钉钉通知中链接宜搭完成业务处置的完成。
(测)工业视觉防错
产线广泛应用工业视觉相机并内嵌算法实现涂胶轨迹、激光焊接质量、装配作业错漏装等异常实时检测,并与PLC进行信号交互,杜绝故障流出,同时将所有图像与总成号进行绑定并存储在本地硬盘,便于后续查看及追溯。
(测)AI视觉手持智能检测单元
替代人工检测,当现场安装人员安装完毕后,使用手持设备在检测安装位置采集图像,软件使用现场局域网将图像传输至现场工控机进行图像结果判断,将检测结果同时显示在工控机与手持设备界面。
三、实施成果
(一)技术应用情况
通过数智化技术与业务深度融合,针对电池&电驱装配线创新打造基于AI-radar“智慧雷达”式的质量风险控制,通过工艺、设备、生产、视觉、质量、人员等数据的采集与建模,使产线制造过程得以孪生,通过对产线孪生的实时监控,实现制造过程的实时可视、主动智慧巡检,保证产线稳定运行,最终打造卓越质量的动力总成产品。(见图2)
新能源装配线技术覆盖情况:
1.电池装配线智慧雷达式质量风险主动管控覆盖情况:针对65个工位的178项质量风险点,通过数智化创新开发应用实现智能雷达式主动质量预防,已覆盖80%,年底实现100%覆盖,最终达成无死角质量管控。
2.电驱装配线智慧雷达式质量风险主动管控:针对88个设工位的156项质量风险点,通过数智化创新开发应用实现主动质量预防,已覆盖70%,年底实现100%覆盖,最终达成无死角质量管控。
(二)行业技术水平
“智问”系统处于行业领先水平,其中多项数智化技术为行业首创。如:“AI视觉标准作业管控平台”、“AI视觉标准作业巡检平台”、手持AI智能检测单元,这些技术都是行业首创应用,并具备一定技术复杂性,通过大量样本数据的不断迭代,准确率与检出率可以满足制造业大批量生产要求,并与行业先进工厂进行对标,技术水平行业领先。(见表1)
(三)知识产权以及标准化
通过专利保护核心技术,通过论文进行知识共享,通过标准固化易于后续横展。
1.共申报2项专利,发表2篇核心期刊论文。
2.获得2020&2021年行业标杆数字化车间等行业奖项2项,并获得2021年度集团科技创新奖一等奖。
3.获得2022年度国家工信部评选的“国家智能制造优秀场景”。
4.建立企业标准1项,建立工厂通用技术标准1项。(见图3)
5.多项数智化应用已在长青、繁荣、蔚山等整车工厂进行横展,如“AI视觉标准作业管控平台”、视频作业监察等。
(四)意识转变、信心倍增
通过“智问”系统的持续应用,事业部业务人员越来越依赖数智化技术,业务人员正从被动接受向主动创新转变,通过这些系统的成功应用,取得了多个奖项与集团领导的肯定,大家对于数智化转型之路充满了信心,这为一汽集团数智化转型打下了良好基础。
(文章来源:中国第一汽车股份有限公司新能源动力总成事业部)